Managing staff absences will be key to the continued smooth running of UK poultry units during the current global crisis.
By Rachael Porter
Staff will be one of the main pinch points in the coming months. And now more than ever it’s vital for egg and poultry producers to update their contingency plans to ensure farming duties can be fulfilled if farmers or staff fall ill.
Agrotop’s poultry consultant Stanley Kaye has planned for other crisis events in his 35-year career, most recently in Israel, but says this time the threat is unusual.
“During extreme weather events or war it’s about logistics – can we deliver a product on time? Do we have road access? But this time it’s about people – keeping them safe and ensuring there are enough staff, with the required skill sets, to work in the supporting industries as well as on the poultry units themselves.”
Poultry units’ increasing reliance on technology and automation is an advantage during the current crisis, but it is also a risk, with even the largest sites often relying on just one unit manager and just a handful of support staff. And that can be a risky, particularly if no one else is up to speed.
But Kaye says poultry producers should use everything at their disposal, and if neccesary units can be run almost exclusively remotely.
“Fortunately the poultry industry is already highly sophisticated, compared to other livestock sectors, in terms of the technology used and the biosecurity measures in place. Now is the time to focus these resources to support and protect staff.”
Working from home
Remote monitoring, through digital technology, has come into its own. “This technology, which is already in use on many units to ensure that many broiler flocks are healthy and efficient and that poultry businesses and run at their optimum 24 hours a day, is proving particularly useful and reassuring to many producers at this difficult time,” says Kaye.
“In a ‘normal’ situation it serves to maximise productivity and bird health and welfare. In the current crisis it has a key role to play in maintaining all these standards and performance when skilled staff may not be able to work on site.
“The current concern is that if a farm manager becomes ill or has to self-isolate it’s not possible for staff with a lower skill set or less experience to step in. And that’s where the technology can take the strain.
“Systems are already in place and the flock can be monitored and managed remotely.”
Red Tractor, which announced in mid-March it was suspending physical inspections due to the coronavirus outbreak has contacted members with updated guidance to answer some of the questions raised by members in response to the fast-moving situation.
“With the possibility of changes to contracts, staff shortages, issues with transport or supplies, we appreciate you may face an extremely challenging few months ahead,” the message to members said.
“It is critically important you have your up-to-date contingency plan in place, so that you are able to ensure all farming duties are carried out, including safeguarding the welfare of your animals should you, your family or your staff fall ill.”
Walking the birds
OPTIfarm’s David Speller agrees and says that with his company’s system in place, if there’s a staffing crisis, producers just need someone – anyone – to walk and check the birds. “They don’t have to be skilled or experienced. We can direct and guide them remotely and, if there’s a problem, the system can identify it and we can advise.
“Someone could walk into a building and tell us it seems stuffy – we can check the temperature and ventilation. We can check, remotely, if feed and watering systems are working properly, for example, and flag that up and tell them how best to fix a problem,” he adds.
“Even culling decisions, if they find a sick or injured bird, can be made with remote advice. Some employees wear a head- or body-cam – so we see what they can see and can talk them through a task. Or we can ask them to send a photo, usually via Whatsapp, and offer support and help. The skills and experience are in place – remotely. All that’s required is someone on the unit to follow instructions and act on the advice given.”
The Derbyshire-based company offers support and advice to poultry units in countries all over the world, including China, the US and Australia. “It’s genuinely a service that’s set up to help and support poultry producers and staff.
“And we’re certainly not in this to exploit producers’ vulnerability at this difficult time,” stresses Speller. “We have a Whatsapp group that’s particularly popular with producers and a great way to share information. And anyone can get in touch with us directly if they need help, support or advice. It’s about ensuring that bird health, welfare and productivity are maintained.
Reaching out
“Anyone is welcome to reach out to us for ‘remote’ help. We’re here to help. And, once the crisis has passed, we hope that some will see the value in having remote monitoring – 24/7 – and continue to use our services.”
Also offering help and support is the British Free Range Egg Producers Association (BFREPA), which sent a letter to all its members when the ‘lockdown’ was announced on 23 March. Robert Gooch told Poultry Business that several members have been in touch with concerns about schooling, with many schools not recognising egg producers as ‘key workers’. In most instances this has been resolved, not least because the list’s wording has been revised to include ‘farmer’ and not just ‘food producer’.
“Clarification was needed and we’ve directed members to who they need to contact to resolve this issue.
“Most free-range egg laying units – more than half – are either run by one person or family run. So staffing itself isn’t an issue if young children are at school and everyone is well. There are jobs that simply can’t be done at all – or safely – in combination with childcare.”
That said, if children can stay safely at home, they should, to limit the chance of the virus spreading.
Egg packaging supplies are also tight and that’s another pinch point for some egg producers – particularly producer packers. Large food service outlets and restaurant chains, including McDonalds, have closed due to the COVID-19 lockdown, and eggs destined for this sector have been diverted to wholesale. This has created a huge and unprecedented demand on egg packaging.
“There are supply chain issues and some producer packers are struggling to source packaging – there’s a time lag,” says Gooch. “It’ll take a week or two to catch up.
“Egg production itself remains steady, which is good news. And consumer demand for eggs, despite the media hype around stock piling, is typical for this time of year.”
Contingency planning: How to keep calm & carry on
Ensure that a least one other staff member, if not all staff, knows the unit manager’s day-to-day tasks and understands the technology and how to access and use it.
On large units, split the poultry management team into two and enforce a strict ‘no contact’ rule. They should work separate shifts or completely separately on the unit. There should be no ‘cross over’ between the two teams or between staff who are key to running the unit.
Close areas where staff can congregate. And, if you have two teams, ensure that each team has its own area for washing, changing, storing belongings.
If you have two key staff members, ask them to avoid the same areas. They should shop in different supermarkets, for example.
Set up a Whatsapp group for all staff and have staff meetings via video conference. There are so many ways to communicate online or via mobile technology – no face-to-face meetings.
Consider offering accommodation to the unit manager on site so they can mitigate the risk of contracting COVID-19. They could also self-isolate on site and still work on the unit, providing they have no close contact with other staff or family working off site.
Access schooling/childcare provision for young children, if required and safe and low-risk to do so, to keep family-run businesses running.
Reach out to companies offering remote or digital management solutions and consider taking on unskilled or inexperienced staff, who can then be guided and supported through this technology.
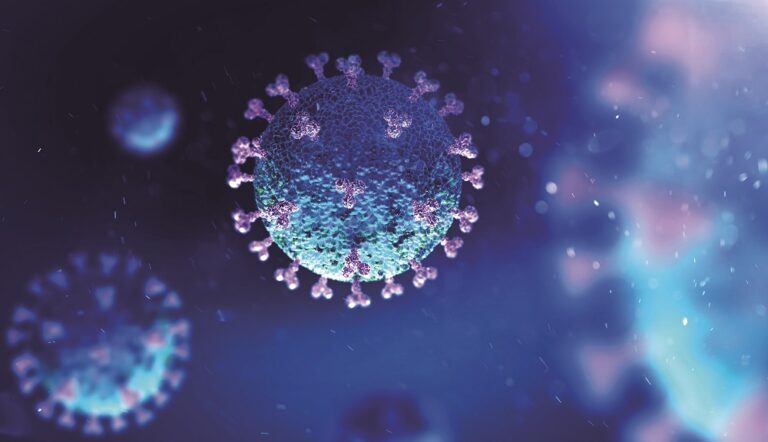
Previous ArticleMoy Park recognised for health and safety performance
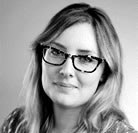
Chloe Ryan
Editor of Poultry Business, Chloe has spent the past decade writing about the food industry from farming, through manufacturing, retail and foodservice. When not working, dog walking and reading biographies are her favourite hobbies.