A Devonshire broiler producer has improved flock efficiency and realised better margins by using real-time monitoring technology and routine data analysis.
Poultry farm manager, David Dos Santos, says he has used Poultry Sense to help achieve one of the farm’s highest margins/m2 through improved flock efficiency.
Dos Santos has managed Chaffcombe Farm, one of Devonshire Poultry’s broiler sites, for over a year, in which time he has sought the support of business owner Robert Lanning to invest in the new technology.
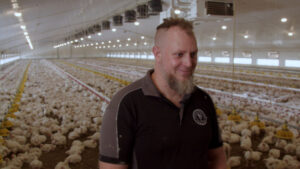
Poultry Sense is a wireless, real-time monitoring system which collects live data. The subsequent analysis of this data allows informed decisions to be made quickly which can lead to significantly beneficial impacts on bird productivity and flock efficiency. The monitoring system consist of air pressure, humidity, temperature and carbon dioxide sensors which can identify small changes in environmental conditions often not picked up by the human eye.
“When I joined the business last year there was clear room for improvement to increase flock efficiency,” says Dos Santos. “The real-time data we have been collecting has prompted major management changes, which have significantly benefited flock performance and overall business performance.
“As producers, we use key performance indicators such as European Production Efficiency Factor (EPEF) and feed conversion rates (FCR) to determine the overall performance of the flock. With the new gold standard EPEF increased from 420 to 440, getting the best from our birds is all about being able to adopt and adapt management strategies according to data collected, and this is why accurate data collection is so critical to our business,” he adds.
“For a shed containing 30,000 birds we would distribute 30 humidity and temperature sensors and three CO2 and lux sensors evenly throughout the house. This allows us to monitor the air pressure, humidity, temperature, CO2, and light levels of the sheds in real-time.”
The number of sensors has enabled the shed to be split into eight zones which increases monitoring accuracy, making it easier to pinpoint specific areas within the shed which need to be improved.
“Since installing the sensors, we have reduced shed temperatures and increased humidity percentages when the chicks first arrive to help reduce the shock and stress on arrival having come from incubators that are 80-90% humidity. By doing this, we have seen improved growth rates from the start, with decreased health issues throughout the duration of the flock lifecycle.
“Using the technology has meant we’ve also achieved our highest EPEF result ever of 426. Although it’s not quite the gold standard of 440, I feel confident we can achieve this within the next year.”
Additionally, the farm’s best FCR results have been seen. “With prices rising, we need to see feed as an investment and being able to achieve better FCR’s means we can be as efficient as possible to maintain profitable margins.”
“The industry is experiencing huge challenges with the increasing cost of production, with energy and feed bills being a particular pinch point. Having improved flock EPEF and FCR means we are improving our margins per meter squared which is undoubtedly supporting business viability at this tough time,” explains Dos Santos.
He adds that after the positive results seen on Chaffcombe Farm, he hopes the technology will be rolled out on the other five Devonshire Poultry units. “With targets such as EPEF set higher, and margins getting tighter, there is no room for error, and so data can help us pick up on things that might go unnoticed and help Chaffcombe Farm remain a competitive broiler producer.”
Read more
Read the latest industry news here