The poultry industry has scaled back production by 10% since Easter due to lack of workers on farm and in plants
On one day in June at the 2 Sisters Willand processing plant in Devon, there were 300 fewer staff on site than were needed to run at normal levels. Production had to be scaled back because there simply weren’t the people needed to operate the machinery. “We physically do not have the people to do the portioning,” said Chris Chater, Hook2Sisters manager of central farming operations. “This is not going away.”
The company may have to consider reducing the number of SKUs it offers supermarkets in order to cope, he added. Catchers are another part of the chain where workers are in short supply. “Ours didn’t turn up on the day they were meant to,” said one broiler producer who supplies the Willand plant. “It’s not for lack of pay because they get close to £40,000 a year; it’s just there aren’t enough around to cope with the amount of work. The price of chicken is going to have to rise as this is unsustainable.”
While there has long been a lack of labour in the chicken industry, the situation is now so bad production has fallen across the UK by 10% during since Easter, according to the British Poultry Council (BPC), which said a shortage of people across farming and in processing plants was now hitting production nationwide.
Entry level roles (requiring a Level 2 qualification) are where the sector is facing greatest difficulty. “We generally operate in areas of high local employment so there is a limit to availability of UK workers and there is negligible appetite from UK workers to move from other parts of the country,” said BPC chief executive Richard Griffiths in a recent article published on the BPC website.
“When it comes to non-UK labour – either from the EU or further afield – we have seen reducing numbers willing to come to the UK, the immigration barriers of salary and skill have been raised way beyond what we can manage, and the cost of bringing people in is being prohibitive.”
The Government’s points-based immigration system came into effect at the start of 2021, which ended free movement of people between the UK and EU. Now, points are assigned for specific skills, qualifications, salaries or professions and visas are only awarded to those who gain enough points. Immigrants now have to meet criteria including earning a minimum of £25,600, and speaking English.
The Government said the change in policy had been designed to “end the reliance on cheap, low-skilled labour coming into the country”. Another factor is the growth in eastern European economies, which had led to more opportunities and wages for workers in their home countries.
Griffiths said the impact of this was now being felt in many industries. “Hospitality is getting much of the media attention but work backwards down that chain: logistics are compromised because of a shortage of lorry drivers, food processors and manufacturers cannot get enough people in factories, farms do not have the people to pick and catch.”
Some poultrymeat businesses have invested more in automation to address the shortage, but this is not a complete solution. “While technology will create higher skilled jobs in the future, we will always be reliant on people,” said Griffiths.
Chater said companies are considering solutions they hadn’t previously had to, including automated catching. “At the moment, I am having to bring in catching teams from the east of England [to Devon]. This is Brexit. Eastern European workers are going home. Morale is really low and tensions are high everywhere.”
Companies are spending money on training to try and attract the right people. All the major integrators are investing in new apprenticeship and training schemes to try and do just that. Soanes Poultry, based in Yorkshire, has set up a new training facility at its factory, for example.
MD Nigel Upson said: “Over the last two years, we have invested £1.5 million to increase capacity due to consumer demand, and now we are having to reduce the number of chicks that we rear because we don’t have the labour to process them. “Brexit and coronavirus have created a perfect storm that has resulted in 1.3 million EU workers returning to their own countries and this has had a significant impact on production. “
In addition to the training hub, we have introduced several initiatives to encourage new recruits, including flexible ‘school day shifts’, refer a friend incentives, and a training website.”
Griffiths said the Government could help ease the problems facing the industry by including poultry meat supply chain workers on the ‘skilled worker list’ and reduce unnecessary thresholds on salaries and skills. He also called for pathways for seasonal workers with minimal administrative burden to support seasonal businesses, which would benefit the Christmas turkey supply chain.
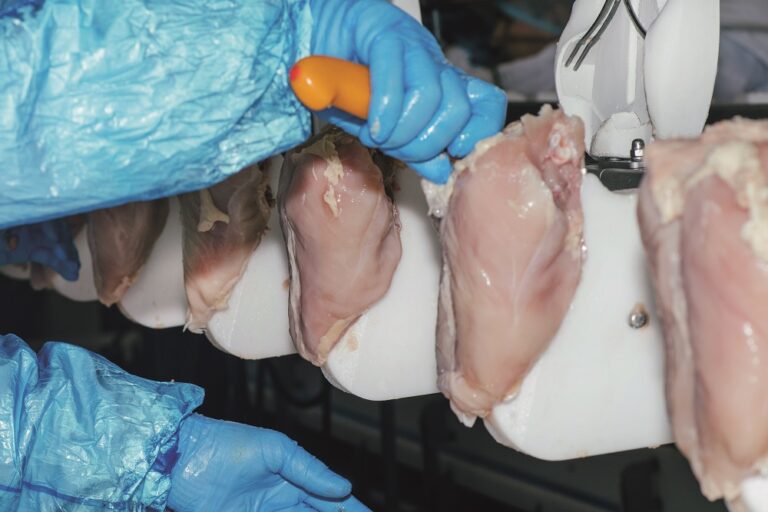
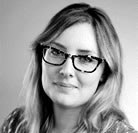
Chloe Ryan
Editor of Poultry Business, Chloe has spent the past decade writing about the food industry from farming, through manufacturing, retail and foodservice. When not working, dog walking and reading biographies are her favourite hobbies.