Traditional Norfolk Poultry is recruiting arable farmers to grow chicken, and has ditched soya from its feed rations
Traditional Norfolk Poultry is on an upward trajectory, with growing demand for its free-range, higher welfare poultry.
In the past three years alone, the integrated poultry business has ploughed £1 million into a Meyn gas stunning system, plus a new evisceration line and a brand-new chilled storage unit.
Last Christmas it shifted a record 400,000 turkeys, all grown in the woodlands of East Anglia using FarmGate Hatcheries genetics, and it is planning to increase numbers again this year.
It is currently processing around 100,000 chickens a week, up from 85,000 just 18 months ago. The chickens are all slower growing breeds, mainly Hubbard 747s and 787s, but also Norfolk Blacks. It is also seeing growth in demand for organic chicken, which comprises 30% of its throughput.
When Poultry Business visited TNP at the start of March, the coronavirus had not yet closed down large parts of the UK economy as it has done now. However, consumers were beginning to turn to supermarkets in anticipation of some of the measures that have now been introduced, and Mark Gorton, TNP’s joint managing director said demand for fresh chicken had risen significantly. Alongside the well reported phenomenon of panic buying soap and toiletries completely unnecessarily, consumers were buying more of everything.
“We’re not big volume producers, so it doesn’t take a lot to make a big difference,” says Gorton. “Another 10,000 chickens a week to us is massive and it only needs a few more people to say, ‘We’ll stay in this weekend and we’ll buy an extra chicken’, before it does filter through and it does make a difference.”
TNP is making changes to make sure the business can respond to more demand. “We’re taking steps to hold a bit more packaging stock as much as we can,” says Gorton. “And we’re talking to our feed suppliers because they’re sourcing some of their raw materials from China so we’re in discussions with them.
“We have a seasonal peak with turkey, so we’re used to bulking up our orders and we have the capacity to hold extra stock, and we’re talking to retailers on a day to day basis about what we need.”
But even well before this current set of circumstances, demand for TNP’s free-range chicken and turkey had been on an upward curve. The business, which won Poultry Business of the Year at the 2019 National Egg & Poultry Awards partly in recognition of its record of investment, had been planning further expansion, both at its factory and on its farms.
And in the past few months it has also continued to take an innovative approach to issues facing the whole industry. Soya in feed is just one example.
Soya reduction
As concern grows about the environmental impact of soya in animal feed, TNP decided to try removing it from its feed rations altogether.
In a series of trials over the past year, TNP fed chickens on a diet based on wheat and cereals, peas and beans, with the soya removed. They discovered that while it was possible to grow chickens entirely without high-protein soya, it wasn’t yet commercially viable because it led to far slower growth.
However, they discovered it was possible to feed the chickens on rations containing soya for the first four weeks of the birds’ lives, then switch to a soya-free ration for the rest of its growing cycle.
“We grow them to maximise them in the first four weeks, it’s the normal chick grower rations, then we slow them down,” explains managing director Mark Gorton. “We have concentrated on the first four weeks of the chickens’ growth, then we grow them a lot slower towards the back end of their growing cycle so we don’t need such high protein rations, so we can take the soya out.”
TNP has now changed its feed across all its free-range chickens and all of its turkeys.
“This is something that has been kicking around for a while, and with our climate change hats on, we’ve been thinking for a while how can we grow chickens with less soya,” says Gorton. “We wondered if we could grow chickens without feeding them any soya, and we have. But that’s probably a little way away from being commercial, it’s just something we tried to see if it was possible and it was.”
Gorton estimates the switch to soya-free rations during the back end of the growing cycle has saved over 700 tonnes of soya over the past year – and it’s been cheaper too. The business sources its feed from Duffields and ABN, which have developed the feed after TNP requested it. “As far as we are aware we are the only ones doing it,” says Gorton. “We haven’t got any exclusivity on it, but we are the only people using it. It’s quite exciting because it improves the quality of the chicken because you allow the bird to grow at its own pace. Certainly, the quality of the chicken I’m seeing in the factory is phenomenal; lovely chickens.”
Contract growing
As demand grows for its poultry, TNP needs additional production on the farms. TNP has dozens of its own farms but has started actively recruiting farmers who have previously never produced chicken before and is offering contracts to grow birds on their own land.
Arable farmers have been targeted in particular. “This is a great opportunity for people with smallish farms of 300-400 acres, who have got children wanting to come back into the business,” says Lionel Halls, who is in charge of recruiting new growers for TNP.
Lack of experience with poultry is not an obstacle. If anything, it’s an advantage. “We quite like getting people without a huge amount of knowledge because we can steer them in the right direction,” Halls says.
The optimum site requires five hectares of land with three houses for a total of 40,000 birds. The growers will be expected to invest around £1 million in constructing the houses, but there are also smaller options.
The project has been designed with help and advice from two colleagues with vast experience of the UK poultry industry – Jim Lambert, who joined TNP as agricultural manager in 2017 after almost 25 years with Cobb, and Halls who has a lifetime’s experience within the poultry industry and who has developed many poultry units across the UK during his career.
“Through the years TNP has built up a vast wealth of expertise in planning and obtaining approval for free range sites, housing, equipment, fencing, tree planting, biosecurity and biomass as well as how to manage birds on free range for maximum welfare and profitability,” says Lambert.
“We will share this expertise with farmers seeking to invest in this type of production. We also have our own academy farm near Ely where we provide residential and day-to-day practical training.”
There has been a good amount of interest in the scheme, says Halls. “I’ve visited well over 100 farmers and explained the process and we have just now had our first crop through on the first farm to have signed up.
“The Middleditches (see case study) are completely new to chicken, and they have achieved everything and more that they hoped for,” says Halls. “With our support and help through the process they are on the road and they have just placed their second crop.”
Seven other arable farmers are currently going through the planning process, but it’s often not a straightforward process. “One of the things we have come up against is a lot of the farmers we’ve looked at get stopped at the first step because of their location near sites of special scientific interest (SSSIs), of which we’ve got an awful lot around us in East Anglia,” says Gorton.
“It’s frustrating when we’re not looking to build huge units,” he adds. “These are 40,000 bird units with a low-density stocking and high cereal percentage food and heavily planted ranges.”
Egg producers wanted
Gorton adds free range egg producers may also make good candidates. “There is not a lot of conversion needed for them to come and grow chicken for us,” he says. “We are offering them a much more stable income. The egg price fluctuates, whereas we are offering them a fixed margin on their chicken in a much more specialised market.
“Some people are a bit sceptical when we talk to them about free-range chicken, because they’ve seen how the free-range egg market has almost become commoditised.
“But with free-range chickens there are set production standards that mean that you can’t really get commoditised. You’ve got minimum kill ages, you’ve got certain feeds you’ve got to feed them, you’ve got certain breeds you need to use, so that protects that market from being driven down on price.”
Can’t get the staff
Like nearly all poultry businesses, which have a high percentage of staff originally from EU countries, TNP employs many non-UK staff.
Although COVID-19 has thrown almost everything into confusion, as it stands at the moment, the Brexit transition period will end on 31 December, and from 1 January, new immigration laws will mean the end of free movement from the EU.
Gorton is enouraging his 200 staff to apply for settled status, which would enable them to continue in their jobs. He has had some success, but says “it’s sometimes difficult to get it across how important these things are.”
“I don’t know what will happen come 1 January,” he adds. “We are not seeing any local people looking for work. We have invested over the years [in automation equipment in the factory] and we have reduced our headcount, and we will continue to do that. But you can’t automate out on the farms.”
Gorton says some roles in particular are hard to fill. “You’ve got your catchers, they start work at midnight and they work through the winter. Where are the local people wanting to do that? We pay good money and overtime, and I don’t know what the answer is.
“And the Eastern Europeans have not taken anybody’s job, it’s a requirement because there is nobody to do those jobs. We haven’t pushed our local workforce away. Why would we? They’ve filled the void. We need these people.”
Processing pinch point
During most of the year, the factory runs smoothly. But at Christmas each year the factory is squeezed by the number of turkeys it processes. More space is needed and so TNP is going to grow even more.
The business has recently been granted planning permission to expand its factory, with £2-£3 million set aside for the project.
“We are heavily investing in the plant,” says Gorton. “The new extenstion will give us a self-contained seasonal turkey operation, which will be used for four weeks of the year then mothballed. It will give us a much bigger area for dispatch and production.”
The new space will also allow it to install new cutting and packing equipment to be used all year round. Much of this will be automated, which is an important step in responding to the lack of available labour affecting food production generally.
“We had a really successful Christmas last year, probably the best Christmas we’ve had. The key thing is delivering the customers’ requirements and I see the turkey business growing again, and it’s the one meal of the year where people don’t want to compromise on it,” says Gorton.
“With the extra capacity we can do a lot more, we have never turned anything down.”
Case Study – Harry Middleditch, arable farmer & contract chicken grower for TNP
Why did you start growing chicken?
“We always wanted to get into the chicken sector because unlike arable farming, which we are in as well, it’s not as volatile and it’s an ever-growing market. It also had the best return of any sector we’d looked at.”
How was the process from start to finish?
“Looking back on it now, it wasn’t too bad. It took about 18 months to get planning permission. You get the standard objections and the surveys and protocol you have to jump through but looking back it wasn’t too bad at all.
“The first batch was a learning curve coming from no background in the poultry sector at all. But TNP were there all the way through and we got through it, the birds hit all the weights, all the targets, and now we are half-way through the second batch. I like to think we know what we are doing. It’s going well. It’s working well alongside an arable farm. It complements it well in the down periods and busy periods.”
What have you learnt from the first crop?
“How to trust the system! With the first batch I’ve learnt to trust that the ventilation, heating, eating and drinking would work. Now I have confidence in the system so there is not so much worry on my behalf.
“With the arable side you’ve got a whole year of growing and remembering what you did year on year, but the good thing about poultry is because you’re getting through volumes of birds and several batches through the year, you can remember what you’ve done with the batch before and improve. Also, there are not so many external variables as with arable.”
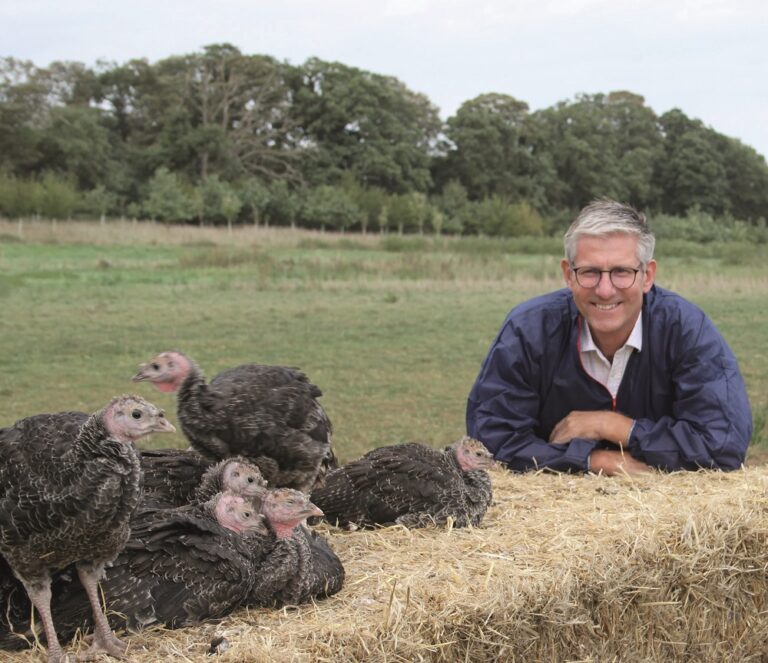
Previous ArticleComment: I’ve never seen anything like this in the egg industry
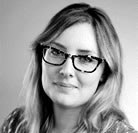
Chloe Ryan
Editor of Poultry Business, Chloe has spent the past decade writing about the food industry from farming, through manufacturing, retail and foodservice. When not working, dog walking and reading biographies are her favourite hobbies.